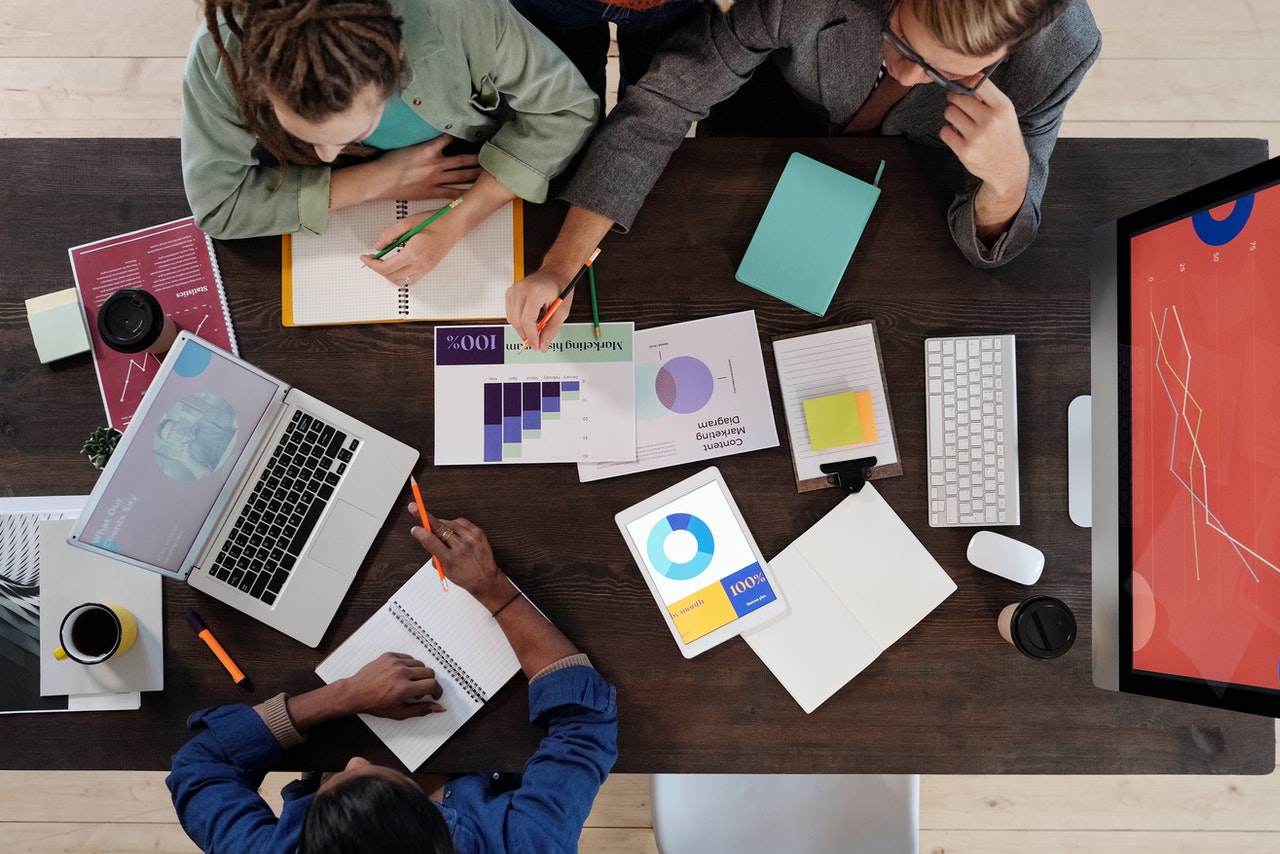
コラム
市場競争に勝ち続けなければならない工場にとって、生産性向上は最重要課題です。それだけに工場管理に携わる工場長や製造管理者の責任はきわめて重大だと言えるでしょう。では、競争力のある工場を作るには、工場管理をどう行っていけば良いのでしょうか。
ここでは、「維持管理」「変換点管理」「方針管理」という3つの取り組みに焦点を当てながら、工場管理のキホンを解説していきます。
8,500名のプロ人材・顧問が登録するプラットフォーム「顧問バンク」。
工場管理・生産管理に知見やノウハウのある人材、人脈を活用した営業活動の強化、社内の経営課題の解決に最適な人材に直接アプローチ!
→まずは、【公式】顧問バンクにアクセスしてPDFを無料でダウンロード
一般に工場管理と言えば、生産計画に基づいて製造全般を統括する「生産管理」や生産ラインをはじめとする現場での作業フローをマネジメントする「工程管理」を真っ先に思い浮かべるかもしれません。また、「品質管理」や「安全管理」「衛生管理」も工場管理の枠組みを構成する重要なファクターです。どの要素が欠けても工場は正常に稼働することができません。すべてがベストな状態に保たれているときに、初めて生産性向上が実現するのだと言えます。
ただし、工場長や製造管理者が工場管理をするうえで最も重視するべきなのは、4M(MAN=人、Machine=機械、Material=材料、Method=方法)の視点で工場の課題を解消し、QCD(Quality=品質、Cost=コスト、Delivery=納期)を最適化して生産性を維持・向上する取り組みです。なかでも目標のQCD(品質・コスト・納期)を達成するために、工場で働く従業員を適切にマネジメントすることは、工場管理において常に求められている課題と言えます。
また、工場管理にはほかにも「所定の人員が所定の持ち場について、与えられた作業を滞りなく安全に遂行する」といった「当たり前」のことを実現することも求められます。そのために必要な取り組みが、次で説明する「維持管理」「変化点管理」「方針管理」です。
完全な無人工場は別として、工場では多くの生産ラインに従業員が配置され、それぞれが所定の持ち場で所定の作業を担います。機械がいかに正確でパワフルでも作業する人に問題があれば、工場は正常に稼働しません。そこで重要になってくるのが「維持管理」「変化点管理」「方針管理」という3つの取り組みです。
工場における維持管理とは、作業員が「当たり前のことを当たり前に行うようにすること」を指します。何が「当たり前」なのかと言えば、「安全・正確・遅れなく・漏れなく」作業させることと言ってよいでしょう。安全性が担保されておらず、どこかでトラブルが生じれば問題解消まで生産ラインはストップし、目標とする1日の生産量を達成できません。
また、作業が正確でなければ欠陥品が発生し歩留まりが悪化します。さらに、個々の能力に合った配置でなければ、ラインのスピードについていけない作業者のところで詰まりが生じることもあります。そして、全作業者が割り当てられた作業を所定の通り遂行しなければ製品は完成しません。
工場長や製造管理者は工場の「当たり前」を阻害する「危険・不正確・遅れ・漏れ」を生じさせないよう日頃から気を配り、必要に応じて作業員に技術講習を受けさせたり、技能検定の取得を支援したりするなどして工場全体のレベルアップを図っていかなければなりません。もちろん、その場で注意や指導を行うのも責任者の仕事です。
作業員が「当たり前のことを当たり前にできなくなった」場合に、それを指摘し正常化を図るのは責任者の役割です。では、正常化のために責任者は何をすればいいのでしょうか?
第一に挙げられるのは、決められた手順やルールを守らない作業者が一定の割合でいることを意識することです。手順やルールが守られないと「危険・不正確・遅れ・漏れ」が生じ、生産計画に大きな狂いが生じかねません。どんな仕事でもそうですが、経験の浅い人間に対しては、すべてを任せきりにするのは危険です。その危険を回避するために、作業手順やルールが細かく定められているのです。
こうした手順やルールを事前に周知しているにもかかわらず、それを守らない作業者がいれば、責任者はこれを注意し、改めてルールを指導しなければなりません。いわば、手順やルール無視といった現場の「異常」を検知して、これを是正するのが変化点管理です。
方針管理とは生産ラインという枠組みを俯瞰して、会社の方針や目的といった観点から工場の生産体制や能力が適正かどうかを判断し、課題があればそれを是正していく取り組みです。
例えば、所定の生産時間を超えてしまったようなケースでは、予定と実績(予実)に大きな差異が生じます。工場の責任者はこうした結果がどんな原因によってもたらされたかを明らかにしなければなりません。工場長や製造管理者にとって、このような問題解決を図る力や業務管理力はきわめて重要と言えます。
半年で約3,500万の利益を出した方法とは?
人脈を活用した「新規開拓営業の方法論」についてはコチラをチェック!↓
ここまで見てきたように、工場とは「当たり前のことを当たり前にできるようにする」ことで正常に稼働します。ただ、この当たり前を維持することは決して容易ではありません。その実現には、QCDが低下する前に現状を的確に把握して解決を図る予防的管理が必要だからです。それには、工場の全体像を常に俯瞰できる体制作りが欠かせません。こうした工場の「見える化」ができて初めて、予防的管理が可能になるのだと言えるでしょう。
工場には改善すべき課題が数多くあります。しかし、上述した「維持管理」「変化点管理」「方針管理」を徹底しつつ改善を実践していくには、人・機械・材料・方法のどこに課題があるのかを発見する知恵が不可欠だと言えるでしょう。ただし、現場からは肝心の課題が見えにくいことも。そんな場合には、多くの現場を経験してきた外部のエキスパートに課題の洗い出しをサポートしてもらうのも一つの手です。
次世代型マッチングサービス「顧問バンク」には、工場管理や業務改善の経験やスキルを持つ人材が数多く登録しています。工場だけでなく、物流や在庫管理など広い視野で業務改善に取り組める顧問に助言を依頼し、現場の生産効率を向上させましょう。
8,500名のプロ人材・顧問が登録するプラットフォーム「顧問バンク」。
工場管理・生産管理に知見やノウハウのある人材、人脈を活用した営業活動の強化、社内の経営課題の解決に最適な人材に直接アプローチ!
→まずは、【公式】顧問バンクにアクセスしてPDFを無料でダウンロード
御社の課題を顧問で解決してみませんか?
顧問マッチングプラットフォーム
顧問バンク
スポット起用から長期まで、「必要なとき」「必要な人数」
課題にあわせて自由に選べる顧問マッチングサービス。
雇用リスクを抑え
即戦力を活用できる
迅速なマッチングで、
あらゆる課題に対応
中間マージン0円優れた
コストパフォーマンス